What are the different types of pumps?
Pumps are devices that move fluids (liquids or gases), or sometimes slurries, by mechanical action, typically converted from electrical energy into hydraulic energy. Pumps can be classified into different types based on their operating principle, the type of fluid they are designed to move, and their specific application.
Submersible Pumps
Submersible pumps are designed to be placed directly in the fluid that needs to be pumped. They are often used in wells, tanks, and other deep bodies of water. Submersible pumps are typically very efficient and can move large volumes of fluid at high pressures.
Rotary Lobe Pumps
Rotary lobe pumps are positive displacement pumps that use two rotating lobes to move fluid. They are often used in applications where precise flow control is required, such as in the food and beverage industry. Rotary lobe pumps can handle various fluids, including viscous liquids and slurries.
Centrifugal Pumps
Centrifugal pumps are the most common type of pump. They use a spinning impeller to create a centrifugal force that moves fluid. Centrifugal pumps are very versatile and can be used in a wide variety of applications, including pumping water, oil, and chemicals.
Progressive Cavity Pumps
Progressive cavity pumps are positive displacement pumps that use a helical rotor to move fluid. They are often used in applications where high pressures and viscous liquids are involved, such as in the oil and gas industry. Progressive cavity pumps can handle many fluids, including slurries and solids.
End Suction Pumps
End suction pumps are centrifugal pumps that have a suction inlet on one end of the pump and a discharge outlet on the other end. They are often used in applications where the pump needs to be installed in a limited space. End suction pumps can handle water, oil, and chemicals.
In-Line Pumps
In-line pumps are centrifugal pumps that have a suction and discharge inlet on the same side of the pump. This makes them very compact and easy to install. In-line pumps are often used in applications where space is limited, such as in booster systems and irrigation systems. In-line pumps can manage various fluids including water, oil, and chemicals.
Self-Priming Pumps
Self-priming pumps are centrifugal pumps that can prime themselves, meaning that they can start pumping even if there is no liquid in the pump casing. This makes them very versatile and easy to use. Self-priming pumps are often used in applications where the pump needs to be primed frequently, such as in dewatering applications.
Chemical & Process Pumps
Chemical and process pumps are designed to handle corrosive and hazardous fluids. They are often made of special materials that can withstand the harsh chemicals they are exposed to. Chemical and process pumps are used in a wide variety of industries, including the chemical, pharmaceutical, and food and beverage industries.
Internal Gear Pumps
Internal gear pumps are positive displacement pumps that use two internal gears to move fluid. They are often used in applications where high pressures and precise flow control are required, such as in the automotive and aerospace industries. Internal gear pumps can handle a wide variety of fluids, including hydraulic oil, fuel, and lubricants.
Liquid Ring Pumps
Liquid ring pumps are positive displacement pumps that use a liquid ring to move fluid. They are often used in applications where high vacuums and low pressures are required, such as in the food and beverage industry. Liquid ring pumps can handle a wide variety of fluids, including water, air, and gases.
Diaphragm Pumps
Diaphragm pumps are positive displacement pumps that use a flexible diaphragm to move fluid. They are often used in applications where precise flow control is required, such as in the medical and pharmaceutical industries. Diaphragm pumps can handle various fluids, including water, chemicals, and biological fluids.
These are just a few of the many types of
pumps that are available at MR Engineering. The type of pump that is right for a particular application will depend on the specific needs of that application.
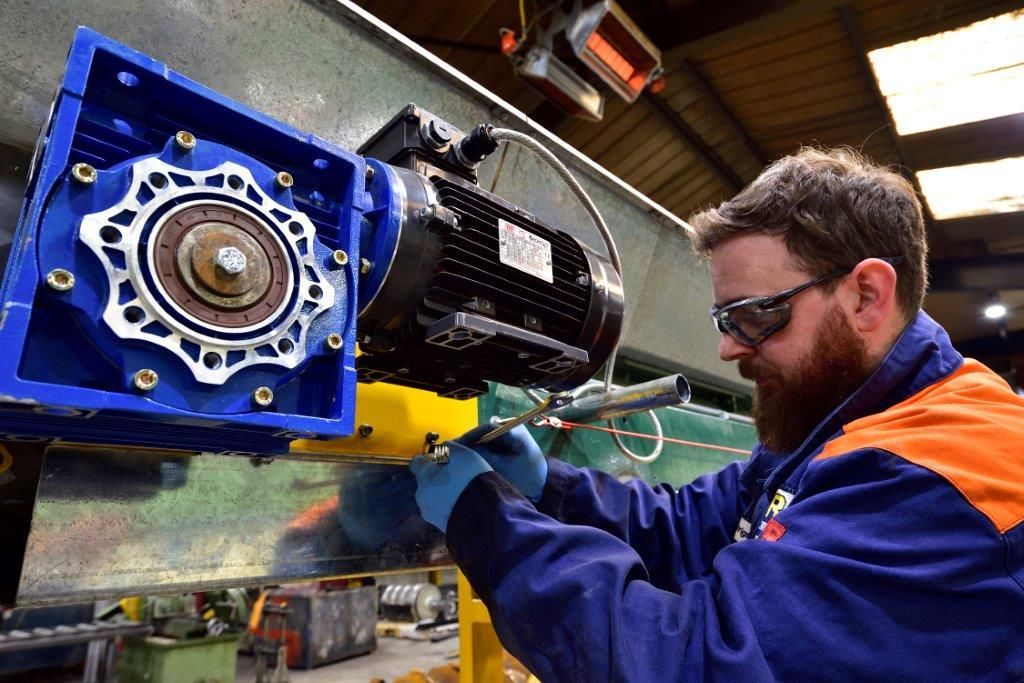