Motor Rewinding Services Merseyside
What is Motor Rewinding?
Motor rewinding is an important aspect of maintaining an electric motor. The process entails repairing or refurbishing an electric motor, which could typically be an alternating current (AC) or direct current (DC) motor. This is done by rewinding its coils or windings. Motor rewinding restores the motor's functionality and efficiency, extending its operational life.
What are the steps in motor rewinding?
1) Before initiating the process of rewinding, the motor is thoroughly assessed to understand and identify the extent of damage or wear. Certain common issues include burnt or damaged windings, insulation failure, or a decrease in performance. Once the damage has been assessed, the motor is then disassembled, with its coils and windings carefully removed.
2) Any damaged or burned wire and old insulation material are stripped away from the motor’s core and coils. The core and coil components are then thoroughly cleaned from any contaminants or dust.
3) After cleaning, new wire (made of either copper or aluminium) is then wound onto the core. The number of turns, wire gauge, and winding pattern must match the motor's original specifications to ensure proper functioning. Furthermore, the winding process must be precise to maintain the motor's performance and efficiency.
4) To protect the motor coil from short-circuiting, after rewinding, insulating materials such as varnish, resin, or tape are applied to the coils to insulate and protect them from moisture and electrical contact.
5) After rewinding and insulation, the motor is then reassembled and all components such as bearings and shafts are attached. At this time, proper alignment and balancing are essential to prevent vibration and ensure smooth operation.
6) It is then essential to conduct rigorous testing of the motor to verify its performance and adherence to the manufacturer's specifications. Testing may include checks for electrical resistance, insulation resistance, and load testing to ensure the motor functions as intended.
7) Finally, after successful rewinding and testing, the motor can be reinstalled in its original application.
Why is motor rewinding needed?
Motor rewinding is a cost-effective way to extend the life of electric motors, especially in situations where replacement is expensive or not readily available. Skilled technicians or motor rewinding specialists perform this process to ensure the motor operates efficiently and safely. Properly rewound motors can provide years of reliable service, increasing their industrial and commercial value and ensuring continuity in the working of the plant and or operation.
Where can you find Motor Rewinding in Merseyside?
MR Engineering provides low and high-voltage motor rewinds and repairs all across Merseyside. We also conduct repair and rewind of submersible pumps. Our repair workshop is able to undertake the complete refurbishment, repair and overhaul of varying rotating plant equipment.
Our offices specifically service all of the Wirral and Liverpool areas, with our experienced team of multi-skilled electro-mechanical engineers providing 24/7 emergency services all year round. Furthermore, we pride ourselves on providing same-day or next-day service, ensuring that all repairing and rewinding needs are met with the highest standards and absolute precision.
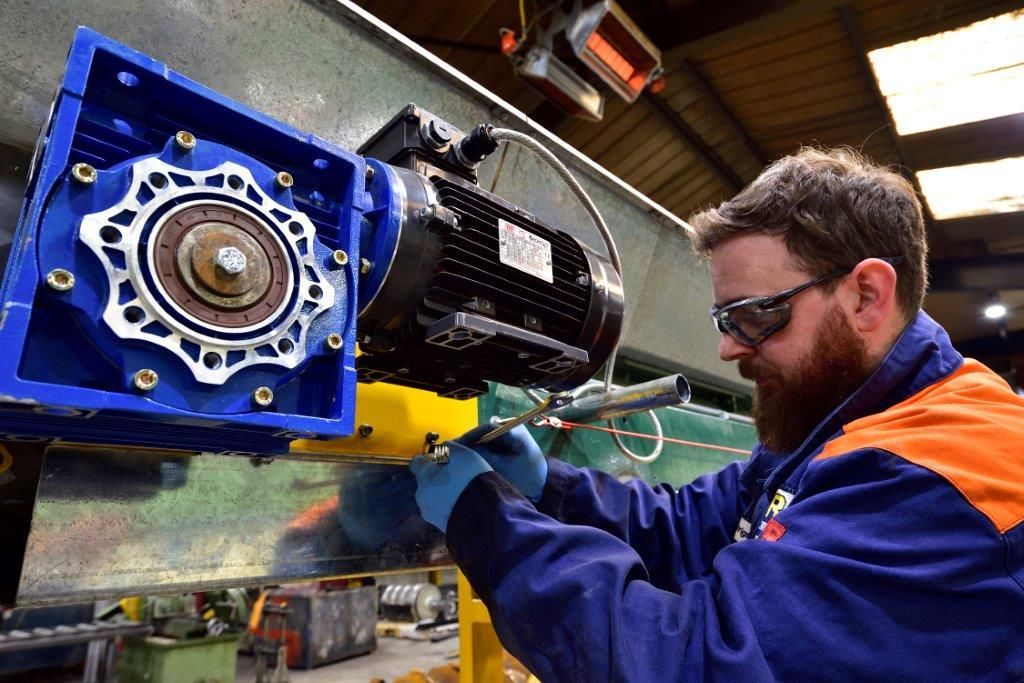